Palen Kimball L.L.C. has provided a host of state-of-the-art preventative maintenance services to its customers large and small since 1932.
We provide customized preventative maintenance service programs for:
- Heating Equipment
- Cooling Equipment
- Energy Management Controls
- Reduced Energy Use and Costs
- Industrial Refrigeration Equipment
We use predictive analysis methods to help identify target areas where preventative measures will produce the most dramatic positive outcomes for our customers – including substantial reduction of the total cost of operation and ownership. This is our unique approach. Time after time, our outcomes far exceed those achieved through more traditional approaches.
Our unique preventative approach can be described in summary as:
- We focus on regularly maintaining equipment as opposed to simply repairing it when it breaks.
- We endeavor to extend the life of your equipment to avoid replacement for as long as possible.
- We reduce your Total Cost of Ownership (TCO) and provide for immediate return on investment by finding immediate cost reductions through energy savings or incentives through our partnerships with energy providers to help offset the purchase price for new equipment.
What will my investment in preventative maintenance services include?
- Labor for planned maintenance, including travel and living expenses when incurred
- Materials for covered equipment such as oil, grease, rags, contact cleaner, etc.
- Regular inspections for worn, failed, or doubtful parts; mountings, drive couplings; oil level; rotation; soot flame composition and shape; pilot and igniter; stem, water, oil, and/or refrigerant leaks
- Testing for excess vibration, motor winding resistance, refrigeration charge; fan RPM; refrigerant oil analysis (acid), water condition; flue gas analysis; safety controls; combustion and draft; crankcase heaters, etc.
- Cleaning coil surfaces, fan impellers, and blades; electrical contacts; burner orifices; passages and nozzles; pilot and igniter; cooling tower baffles, basin, sump and float, chiller, condenser, and boiler tubes.
- Regular adjustments or replacement of equipment components such as:
- Aligning belt drives, drive couplings, air fins, etc.
- Tightening electrical connections, mounting bolts, pipe clamps, refrigeration piping fittings, damper
- Adjusting and checking belt tension, refrigerant charge, super heat, fan RPM, water chemical feed and feed rate, burner fuel/air ratios, gas pressure, set point of controls and limits, compressor cylinder un-loaders, damper close-off, sump floats, etc.
- Lubricating motors, fans and damper bearings, valve stems, damper linkages, fan vane linkages, etc.
- Filters for equipment listed in inventory of covered equipment are included
- Belts for equipment listed in inventory of covered equipment are included
How do we get started?
Step 1: Evaluate the current condition of your facility and equipment and conduct an energy audit.
Step 2: Develop a customized Preventative Maintenance (PM) program for existing and for any new equipment that will be purchased in order to eliminate unscheduled breakdowns and unplanned outages and to maximize life expectancy.
Step 3: Identify equipment that should be replaced rather than entered into the PM program.
Step 4: Identify and secure all available rebate, discounts, or incentives with energy providers and partners in order to most quickly and effectively decrease your energy usage costs and/or develop a custom plan to reduce energy usage costs which, in combination, will help to offset the cost of any new equipment purchases.
Step 5: Implement the programs!
We're a Marsden Company!
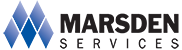